Why BlueScope is leading the decarb race
Steel is the world’s most important engineering and construction material. Unfortunately, producing steel accounts for 8% of global CO2 emissions. Decarbonising steel will play an important role in helping the world meet its emission targets.
In this Firetrail ESG Insight, we explore the topic of ‘green steel.’ We find that the technology for green steel exists, but that its adoption requires:
- New steel mills
- Cheap, green hydrogen
- New, high-grade iron ore mines
For these reasons, we conclude that green steel is a long-term solution to the industry’s emissions. In the next decade, most emissions reduction will come from decarbonising existing mills.
To illustrate the pathway to net zero, we discuss BlueScope Steel’s approach to emissions. BlueScope (ASX: BSL) is Australia’s largest steel producer and a core holding in Firetrail’s Australian High Conviction Fund.
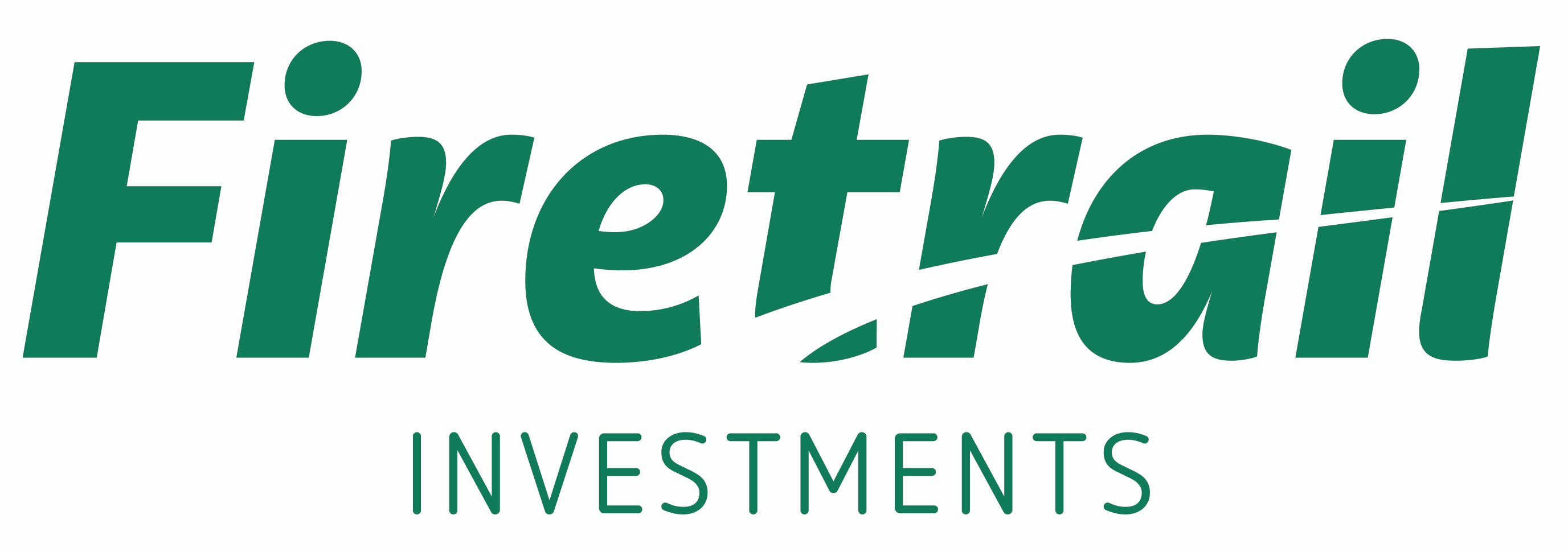
To start off, let’s go over some steel production basics
Steel is an alloy (mixture) of iron and carbon. Carbon is introduced to increase steel’s strength but typically accounts for less than 0.3% of steel’s total weight. Approximately 1.9 billion tonnes of steel are produced each year, with more than half produced in China.
The two main manufacturing methods used to produce steel are:
- Primary production using iron and coal in a basic oxygen furnace (BOF)
- The recycling of scrap steel in an electric arc furnace (EAF)
Figure 1: BOF vs. EAF: Share of production and emissions
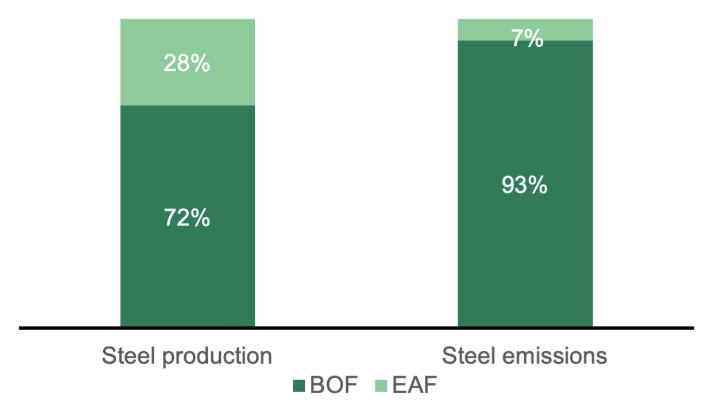
Source: Worldsteel Association, Midrex
Our discussion will focus on BOFs, which produce primary (‘new’) steel and have the highest emissions intensity. Most steelmaking emissions occur in ironmaking, due to the use of metallurgical coal. The primary purpose of coal is to create a chemical reaction that reduces iron ore (Fe2O3) to iron (Fe).
Carbon Steel: Fe2O3 + C > Fe + CO2
Carbon (C) is contained in coal
Figure 2: BOF steelmaking process. Most carbon emissions occur in the ironmaking stage
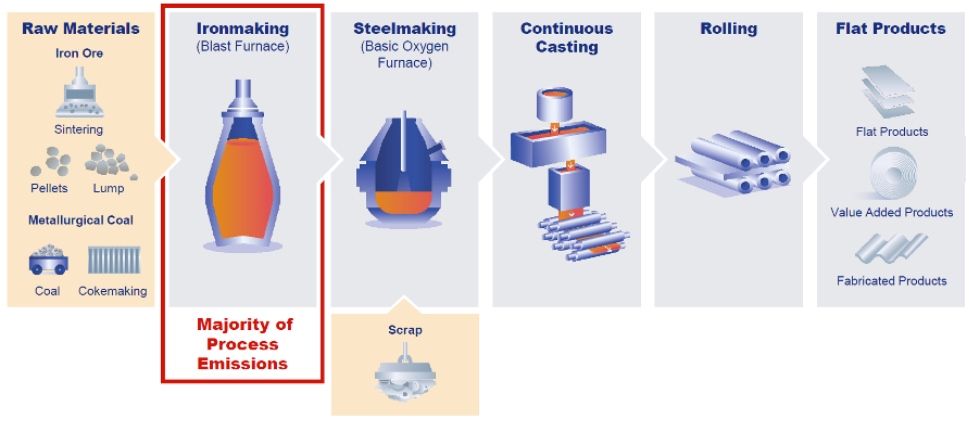
Source: BlueScope
Coal has two other purposes. Firstly, it adds the extra carbon needed to make iron into steel. Secondly, it generates intense heat, allowing iron to remain in liquid form and pour out of the furnace. Keeping iron hot enough to flow is critical; failing to do so can cause considerable damage to furnaces.
Despite its usefulness, coal releases substantial amounts of CO2 into the atmosphere. The key to reducing steel emissions is to find an alternative to coal.
Green steel is a proven way to replace coal with hydrogen
Green steel is touted as the solution to eliminating steel’s carbon emissions. It uses hydrogen (H2) as a substitute for coal in ironmaking. The process produces water as a by-product instead of CO2.
Carbon Steel: Fe2O3 + C > Fe + CO2
Green Steel: Fe2O3 + H2 > Fe + H2O
It is a proven process, with Swedish steel producer SSAB delivering its first green steel product to Volvo in August 2021. However, the steel was produced in SSAB’s pilot plant and is not yet commercially available.
Figure 3: Green steel produced by Sweden’s SSAB
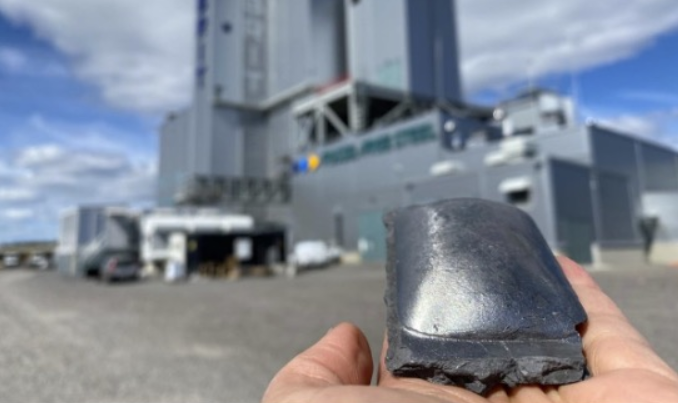
Source: SSAB
SSAB aims to start commercial-scale trials in 2025 and be successful by 2030. If successful, the company will transform its current operations to green steel.
Three key challenges for green steel
Although the technology may soon exist to mass-produce green steel, its adoption faces three important challenges:
1. The need for new steel mills
Green steel is not produced using the same process as conventional steel. Today’s BOFs would need to be effectively replaced or rebuilt to make green steel. The capital cost and business interruption associated with doing so are prohibitive. Green steel will therefore be produced in new mills, while legacy mills are phased out.
Bloomberg New Energy Finance (BNEF) estimates that 56% of primary steel needs to be green by 2050 for the industry to achieve net-zero emissions. Conventional mills will remain part of the mix but will require abatement and offsets to be carbon neutral. The remaining emissions are reduced through greater use of scrap steel.
Figure 4: Green steel accounts for 55% of new steel in 2050
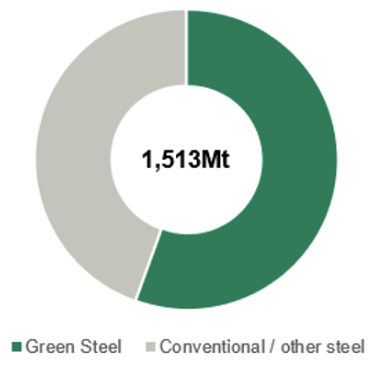
Figure 5: Production – increased scrap also plays a major role in reducing emissions
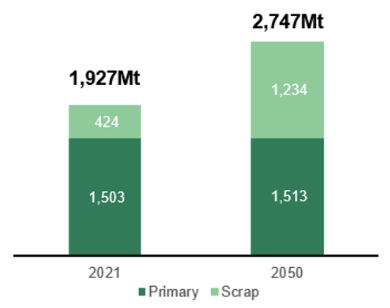
Source: BNEF
BNEF’s scenario illustrates that green steel is critical for the industry to reach net-zero. However, it is part of the solution, and will be phased in as new mills are built, or where existing mills can be refurbished. The transition is likely to occur gradually, over an extended period.
2. Green hydrogen
Green steel requires cost-competitive ‘green hydrogen.’ Green hydrogen refers to hydrogen that is produced with renewable energy. The process is relatively simple but requires significant amounts of electricity. Transporting hydrogen around the world is expensive. It must be cooled to minus 253°C to travel on ships or converted to ammonia.
For green steel to achieve widespread adoption, green hydrogen needs to be cost-competitive and available at scale. We believe that green hydrogen has a future but recognise that it will take time to be developed.
3. High-grade iron ore (magnetite)
High-grade ore typically exists in the form of ‘magnetite’, while lower-grade ore is in the form of ‘hematite.’
Magnetite’s high grade and low impurities are necessary for green steel. However, magnetite accounts for less than 15% of iron ore traded on the seaborne market, and only 25% of iron ore resources in Australia. It is also more complex and costly to extract.
Figure 6: Australian ore bodies
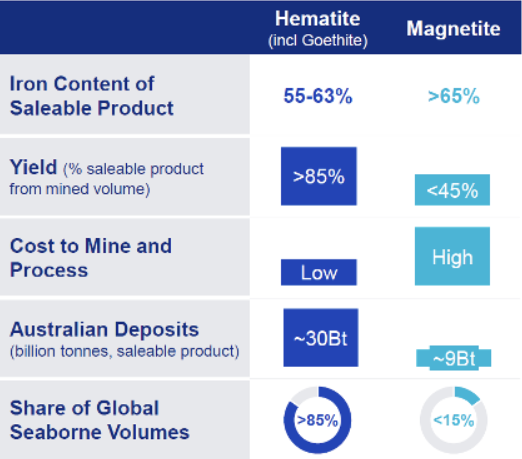
Source: BlueScope
BNEF estimates that for the world to reach net zero by 2050, we need to mine approximately 890Mt of magnetite per year. This is ten times the quantity that is mined today.
To get a rough sense of the investment required, the cost to build Rio Tinto’s 43Mt Gudai-Darri project was $4.5 billion. Extrapolating this figure to BNEF’s estimate implies costs in the order of $100 billion.
Much of this capital would be incurred in any case, as new iron ore projects are needed to replace old ones. The challenge is committing miners to large magnetite projects without certainty that steel mills will move to green technology.
To summarise, the adoption of green steel will be gradual. Widespread adoption will require new steel mills, lower cost green hydrogen and new high-grade ore mines.
Net-zero pathway for BlueScope Steel
Green steel is an exciting prospect but should be thought of as a long-term solution. In the meantime, companies must seek pragmatic ways to reduce their emissions.
BlueScope is doing just that. Management recently hosted Firetrail and other investors at the Port Kembla facility and outlined the company’s emission targets.
Figure 7: BlueScope Scope 1&2 emissions intensity – tonnes of CO2 per tonne of raw steel
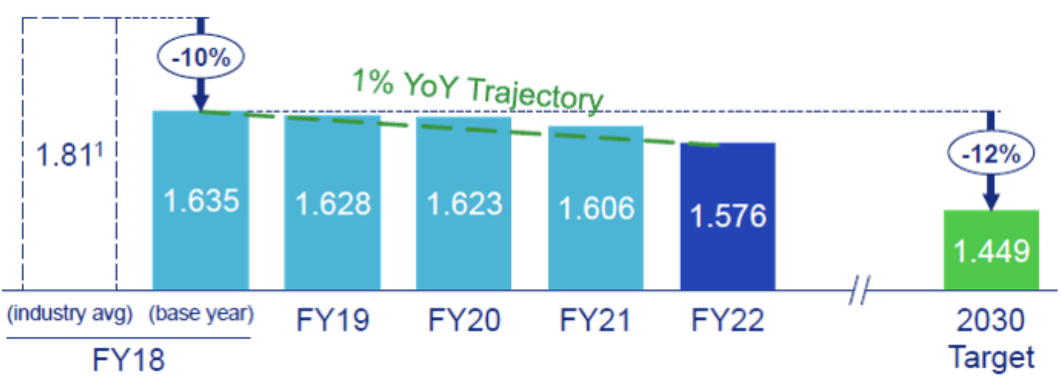
Source: BlueScope
BlueScope’s emission intensity is 10% less than the industry average. The company is targeting a reduction in emissions of 12% by 2030 (from FY18 levels). They aim to achieve these targets primarily through:
- Improving process efficiencies
- Using lower-carbon energy sources
- Increasing the use of scrap
Figure 8: BlueScope – path to net-zero
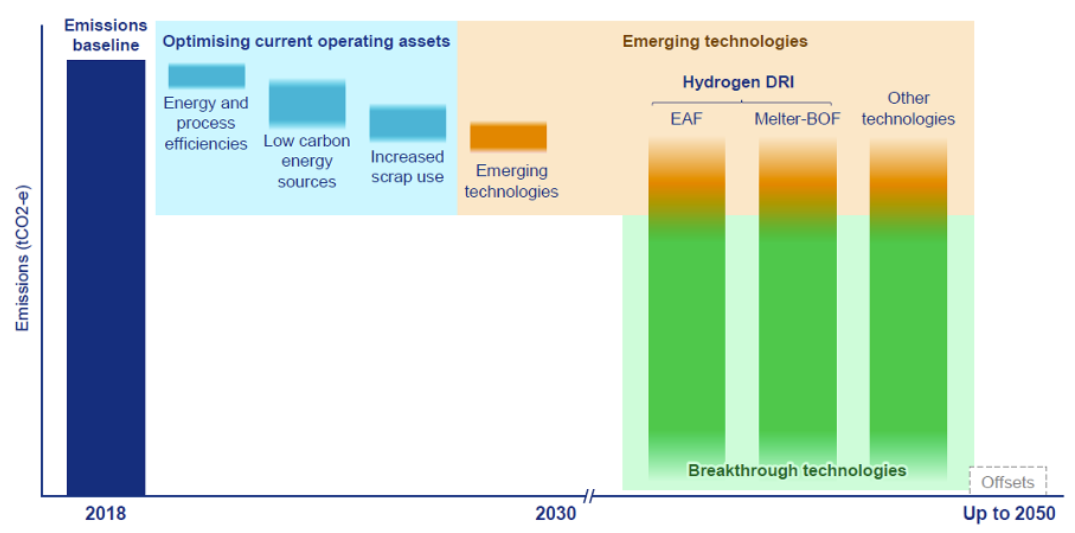
Source: BlueScope
Beyond 2030, breakthrough technologies such as green steel are necessary to meaningfully reduce emissions. BlueScope recently partnered with Rio Tinto to produce green steel using a pilot plant. The company also has a partnership with Shell to explore options for green hydrogen production in Port Kembla.
Through these initiatives, we believe that BlueScope has struck the right balance; focusing on what can be done immediately while remaining committed to longer-term solutions.
Conclusion
The steel industry is fundamental to our lives but contributes significantly to global CO2 emissions. Finding an alternative to coal is the only way to meaningfully reduce emissions from new steel production.
Green steel is an exciting prospect but faces challenges, both in terms of technology and raw material availability. There are three key hurdles to the widespread adoption of green steel:
- The need to build new steel mills
- Cheap, green hydrogen
- New, high-grade iron ore mines
We believe that BlueScope is making good progress in reducing emissions with the technology currently available. We will continue to monitor advancements in green steel technology and engage with the company as it progresses along its decarbonisation roadmap.
Discover more about high-conviction investing
Firetrail is an investment management boutique that specialises in high-conviction investing. They build concentrated portfolios of their best ideas, to generate outstanding long-term performance for their clients. Click here to find out more.
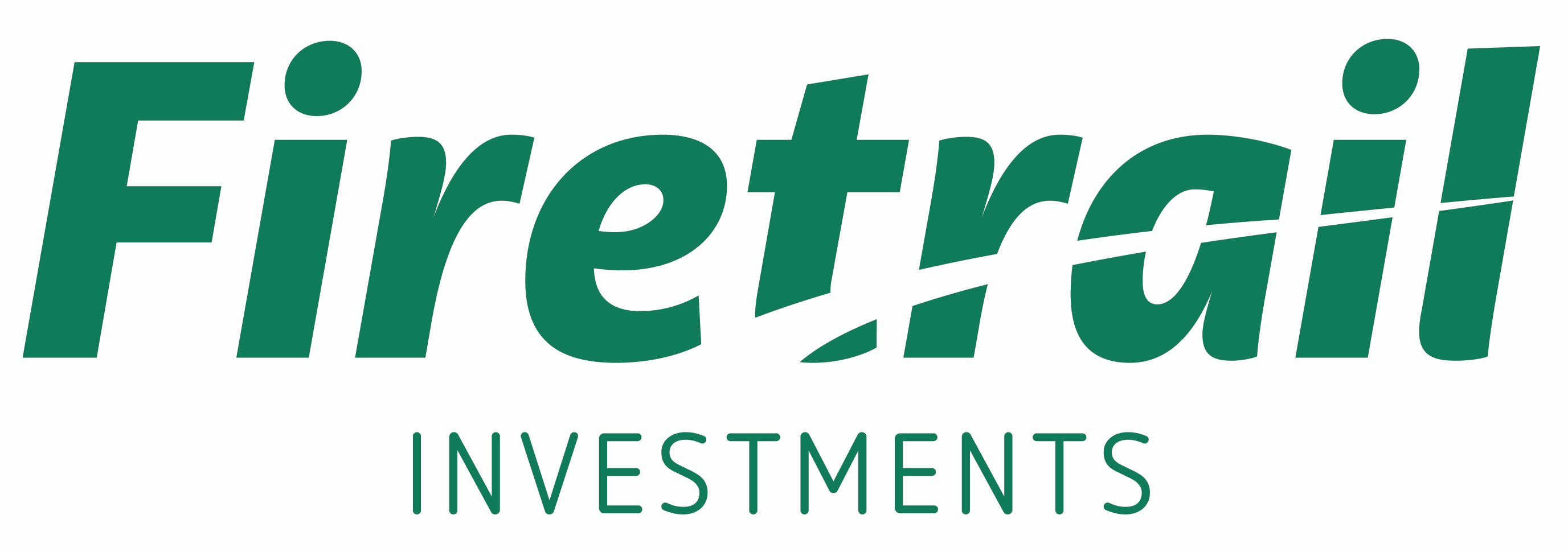
1 stock mentioned
1 fund mentioned